In a theoretical world, building a tool goes step by step and
works mistake free upon completing the last detail. Unfortunately, this is not always so in the real world. Complicated
tooling, which has many variables, does not always perform exactly as expected when completed. This is a situation where
B&J Specialty has a solution to determine the cause of undesired results. We often assist our customers by scanning
existing tooling and comparing it to their 3D CAD model with Rapidform XOR. The output from that overlay is used to
diagnose and repair the tooling so it works properly (see below).
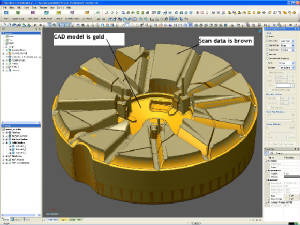
A plastic injection mold insert was not sealing
off properly when the mold was in closed position. The insert in question was scanned to see if the insert matched the
current CAD model data. Upon overlaying the scan and CAD data in Rapidform XOR, a sizable amount of steel was present
on important shutoff surfaces. By using the color mapping analyzation, we could determine the amount of steel that needed
to be removed for proper function of the insert. (Click on images to enlarge)
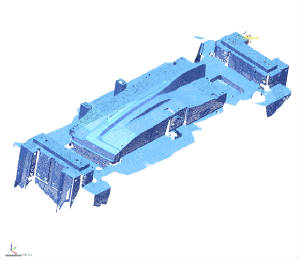
A large hot stamping die was producing non-conforming
parts. We scanned the upper and lower halves of the die. The scan was overlayed onto the CAD data. Upon
inspection of the lower assembly, we noticed a considerable steel heavy condition existed. The excess stock was removed
in our Okuma bridge mill. The removal of the steel alleviated the problem and our customer was producing acceptable
parts in a matter of days. (Click on images to enlarge)
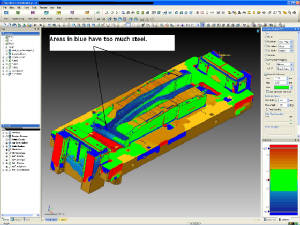
|